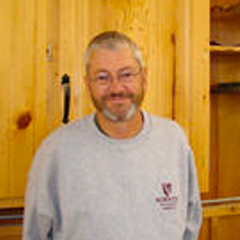
Cabriole Legs: How to Build a Classic
David Munkittrick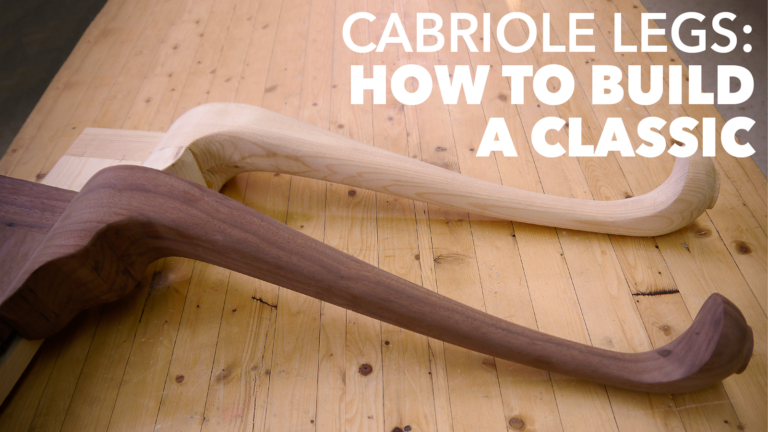
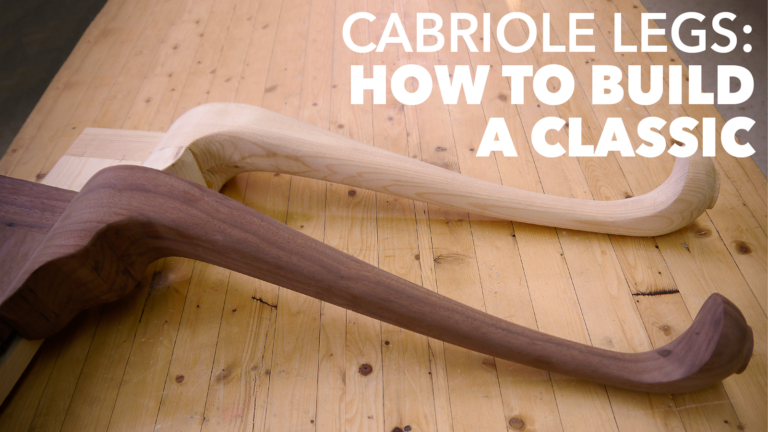
- In-depth Instruction; over 55 mins
- On-demand video access anytime
- Bonus downloadable PDF resources
- Access to class Q&A
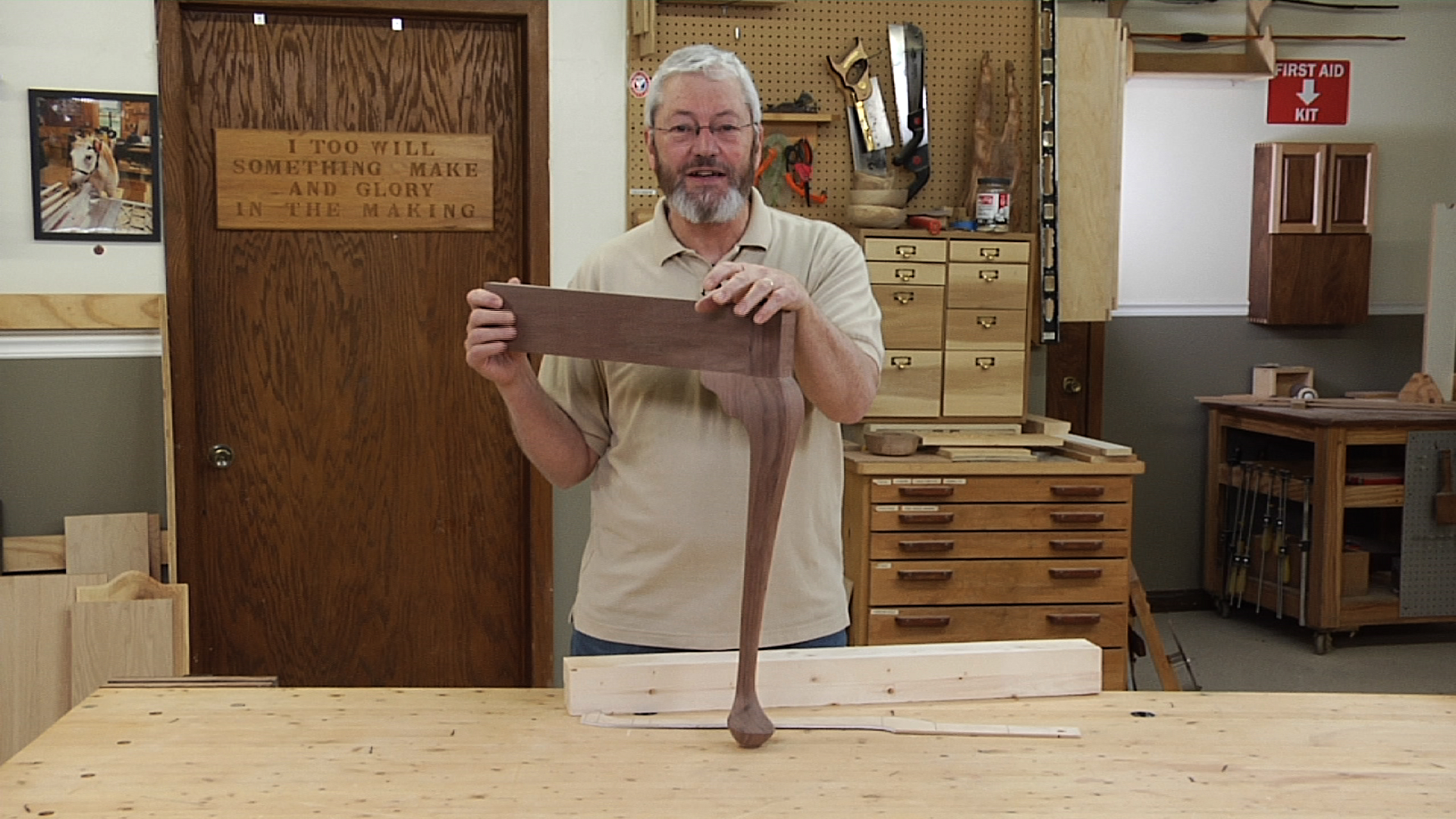
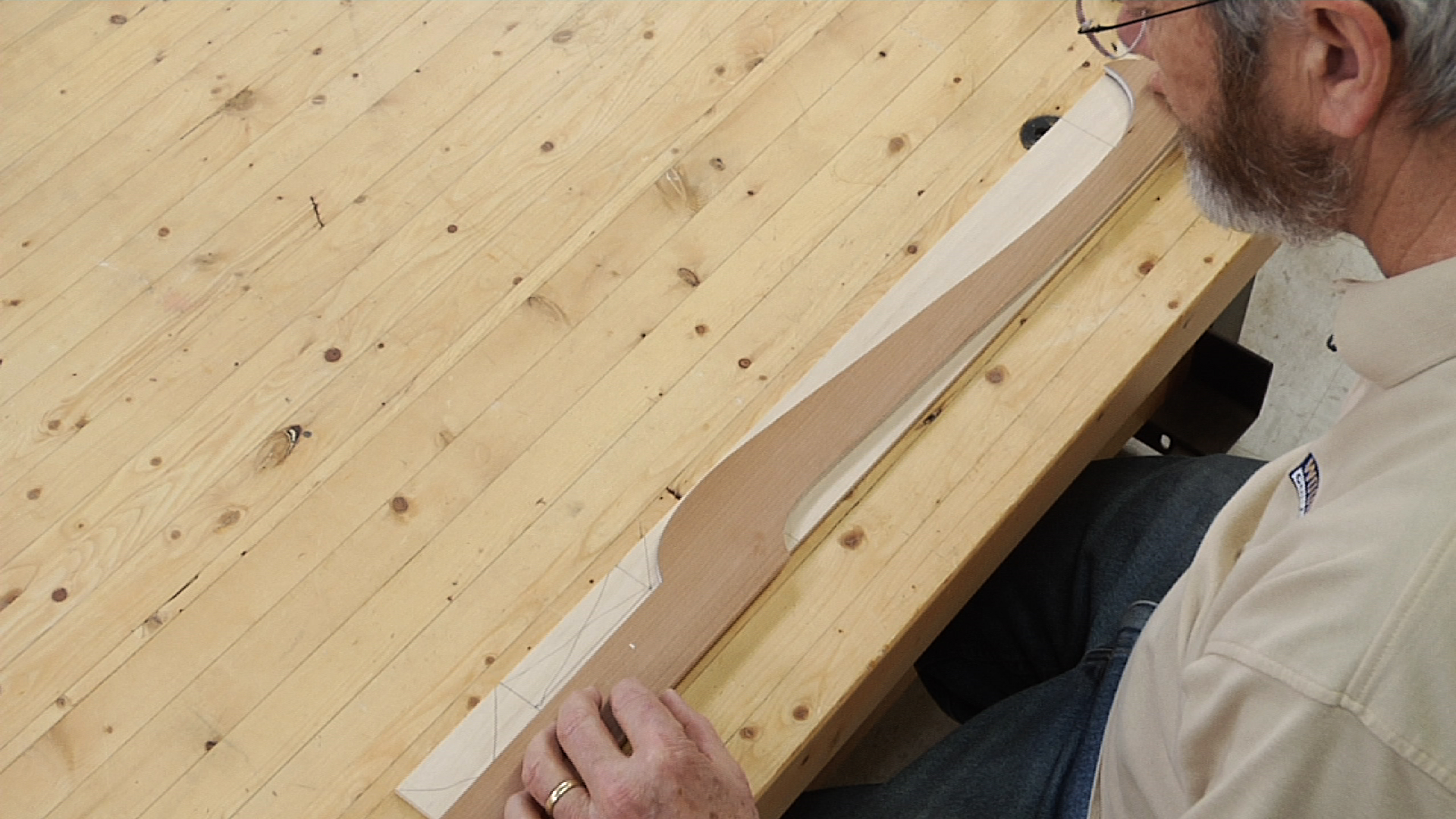
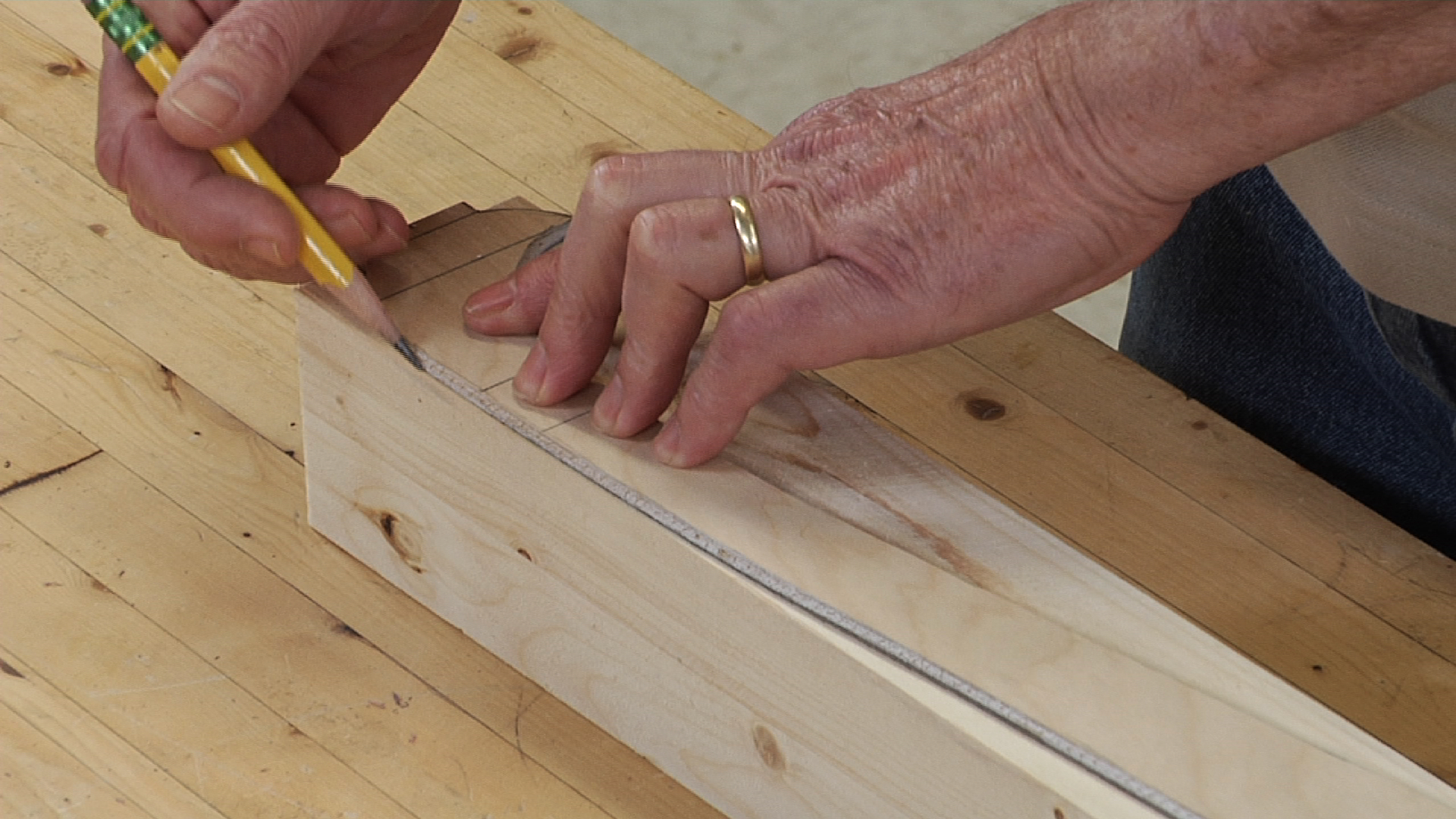
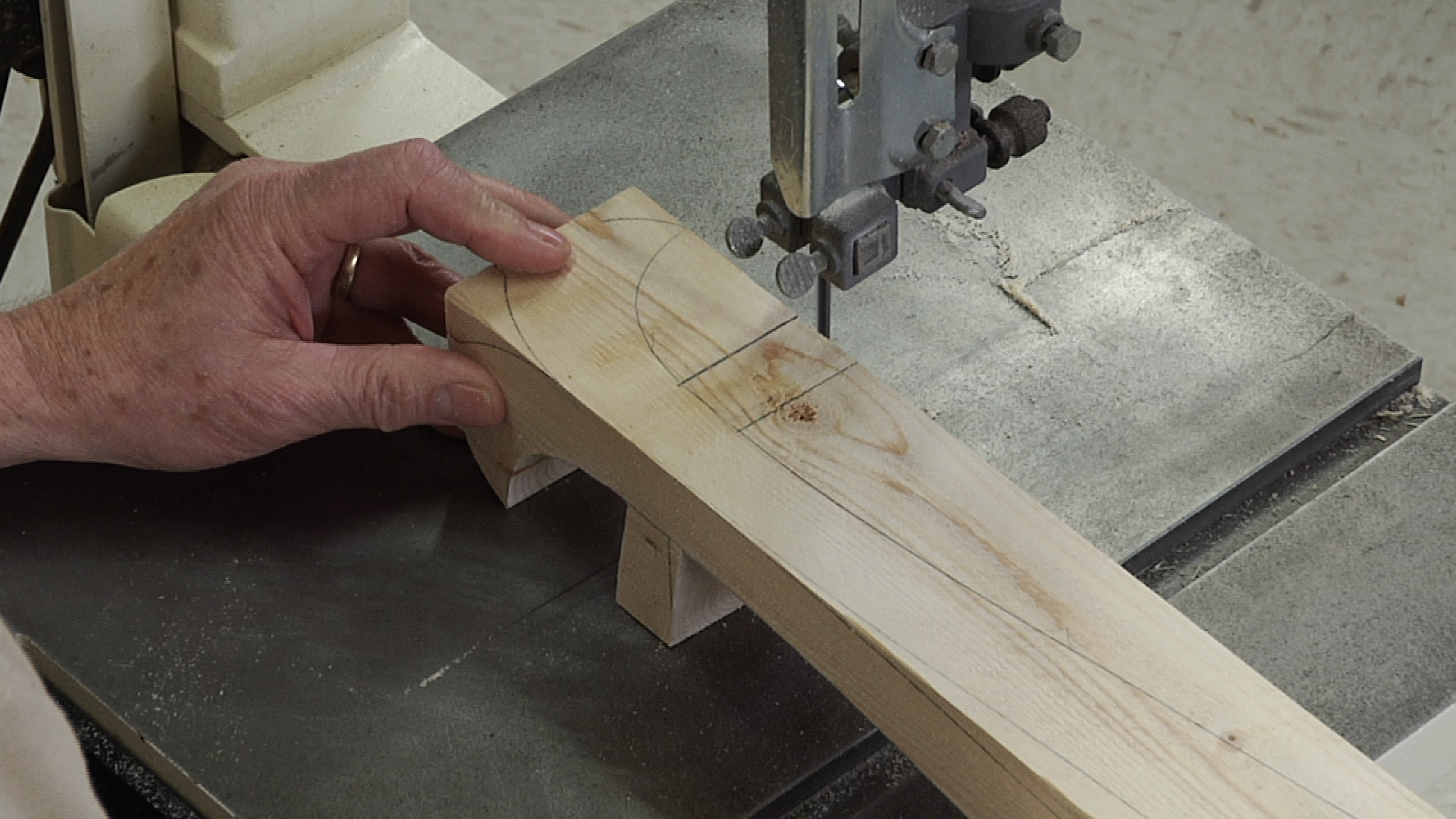
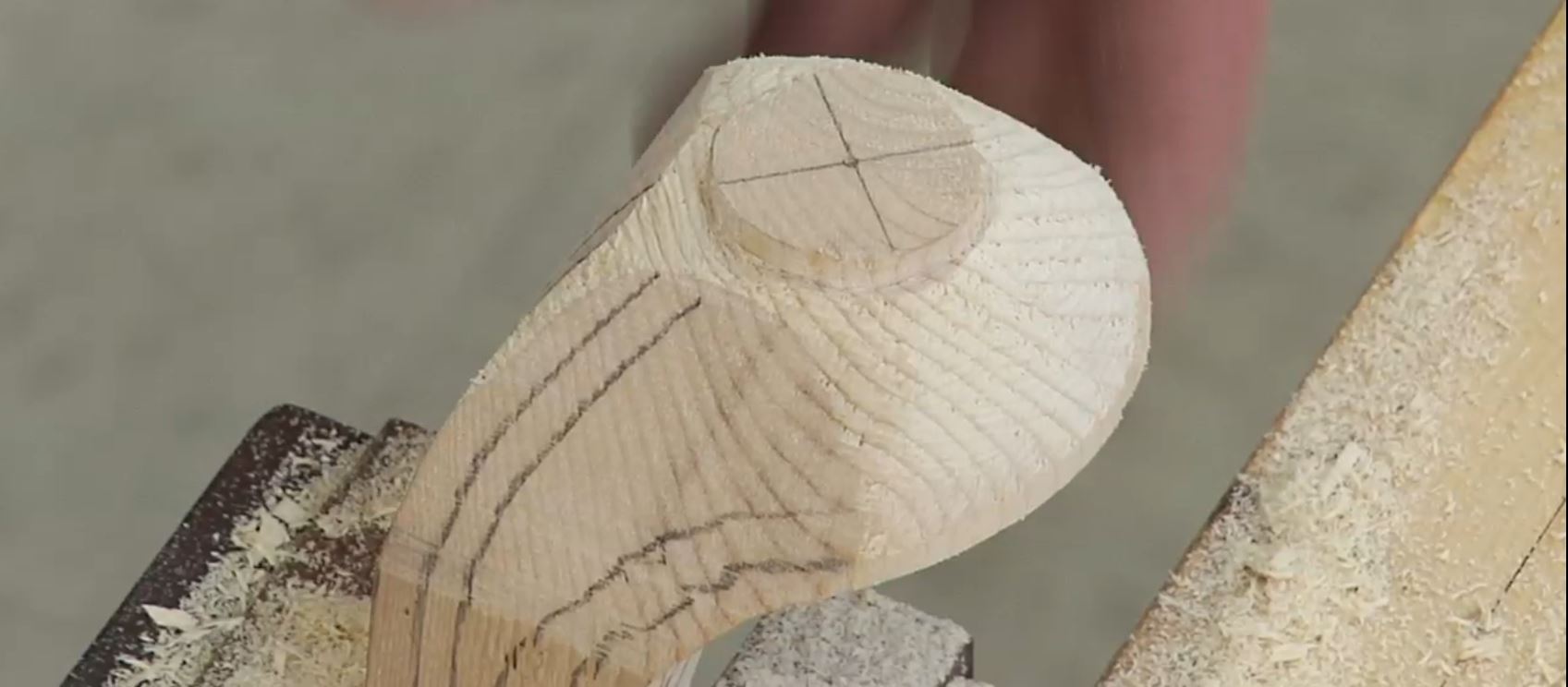

Description
Along the way you’ll learn about the power and hand tools you must have, the tools that are nice to have, and how to use them all.
The Class is full of tips and tricks that help you smoothly navigate the process of creating this iconic leg design, including:
- How to choose the proper grain selection for your leg stock
- Tips for successfully drawing free hand curves
- Rules of thumb that guide you in laying out your own cabriole leg design
- How to safely cut a curved three-dimensional object on a bandsaw
- Sure-proof guides for successfully hand shaping the rough cut leg
- How to cut and fit a transition block with a perfect grain match
If you’re anxious to get right to the leg making, you can skim the design and layout section and use one of the three ready-made templates included as extra material in this Class package. Simply print out the desired leg profile and transfer the shape directly to your template stock. No drawing or measuring is required.
This Class is sure to add a new dimension to your woodworking skills and capabilities.
David Munkittrick
David Munkittrick lives in western Wisconsin and has been woodworking as a professional woodworker for 25 years. His property contains an old pig barn that he retrofitted to use as a woodwork shop. Over the years, he has had the opportunity to write numerous magazine articles for various publications on woodworking and home improvement. His passion is to build furniture and cabinets and tell the world of his experiences. He is continually amazed at the breadth and depth of woodworking throughout the world we live in. He sees his job as helping others get the information they need to develop their skills, make wise buying decisions and make their woodworking endeavors a success. (Photo by Mike Krivit)
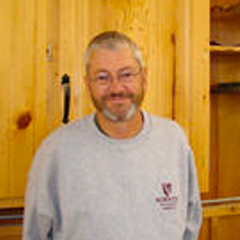
Bonus materials available after purchase